7 tips for better Fabric Cutting Room Productivity
by Coats Digital

Besides having high-performance precision machines, can we take any measures in order to save the fabric cost? Let’s find out…
With the help of automation, the cutting room has become one of the most advanced departments in an apparel manufacturing facility. Here, out of the total material cost, the fabric cost represents 50% to 70% of the total production cost. Since reducing this fabric cost is not something under the control of manufacturers, reducing the amount of fabric used is something they can work upon. For a factory to gain an edge over its competition and increase profits, fabric usage needs to be done smartly.
Automated spreading machines significantly reduce the workload of the spreading operator and increases productivity. Fully automated knife cutting systems are perhaps the most effective means of cutting fabric. They ensure sufficiently high quality and accuracy, as well as, very high productivity for both low-ply and high-ply cutting processes. With the help of automation, advanced fusing presses perform a very sensitive fusing process to ensure high-quality fused composite and avoid textile material shrinkage.
But besides having these high-performance precision machines, can we take any measures in order to save the fabric cost? LET’S FIND OUT!
1. Preparation of a good cut plan
To increase material utilisation, cut plans should be prepared based on different limitations provided for the ease of operations. Sometimes, these limitations are from the customer, such as:
- length of the table,
- maximum / minimum no. of garment to be put in the marker,
- the garments allowed to be cut in pairs only,
- maximum / minimum no. of plies to be put in the lays,
- markers in multiple of certain marker, and
- extra pieces allowed to cut over target quantity.
Making a manual cut plan adhering to the above limitations is a tedious task. It becomes even more tedious when you have dozens of orders lined up on a daily basis. On the top of that, manual processes are prone to human error and have lesser consistency in terms of giving good results.
2. Preparation of relevant patterns and markers, and cutting on the floor
After the process of fabric inspection, the cutting department begins with fabric planning. Here (depending on the cut-plan and fabric grouping) the cutting department can give the pattern maker (CAD department) instructions on what shrinkage should be used for which size set.
These instructions can be provided by summarizing all fabric roll information i.e. width, shrinkage families, in certain range and sometimes, shades. This helps in avoiding preparation of redundant patterns. The same information must be available to the person laying the fabric on the cutting floor. This can help the department to keep a check on the cutting operations and minimise mistakes in order to get the planned output and to meet the daily targets.
3. Grouping of width
The concept of width grouping is simple. Width grouping is done to utilise variable width across the fabric rolls and maximise savings in fabric consumption. Following are the ways that can be practiced for width grouping:
(i) Group fabric based on actual width: several width ranges can be grouped into one group and thus width groups can be identified over a certain jump of width. This jump is called width offset or width range.
(ii) Same ratio marker made on multiple widths: Quantity of fabric in each group is known which helps in calculating the number of garments that can be cut from that group. Thus plies can be distributed over the different width markers accordingly.
To have better fabric consumption, prepare only relevant markers with specified widths instead of making markers with the minimum width fabric. This practice monetises on the actual width available hence maximising utilisation.
4. End-bit utilisation
Different markers have different lengths and so do the fabric rolls. This creates a wastage opportunity where every fabric roll tends to generate a minimum of one end-bit (an end-bit is a fabric piece smaller than the lay length, left after roll completion). It is important to fully utilise the end-bits in order to reduce wastage.
These end-bits have to be grouped as per lengths and markers have to be made accordingly to efficiently utilise them. The thought seems simple but may get complex while execution. With hundreds of rolls and dozens of markers, the number of possible combinations are infinite and thus reaching to a perfect combination is a difficult task.
This is the case for one order. Can you imagine the same for a cutting floor where huge volumes of orders are planned and executed daily The effort of doing this task manually is huge and nearly impossible.
5. Meeting packing ratios
Every Purchase Order comes with a pre-specified packing ratio. The lay-wise output may not always conform to this ratio which adds another dimension to the problem. But what if the plies per lay are pre-set to conform to this ratio? This can be done by allocating the number of plies at the lay-planning stage itself.
6. Detailed reports
Fabric reconciliation can be a huge problem once the production starts. Damages in fabric lead to a shortfall in production unless a damage allowance has already been incorporated. Even in a case where allowance is incorporated, it is done at the fabric buying stage by accounting for an overall wastage percentage. This allowance is highly variable.
Laying of fabric for cutting, sewing and fabric stocking should take place concurrently to enable continuous production of garments without a break. The reports should be elaborate and should include all the attributes of the uses to have clear picture of the fabric stock and its consumption. The same report should be available for future references for any similar orders, which in-general is again a very tedious task to manage.
7. Defect tracking and reducing defective garments
At the time of finishing, defects concerning measurement problems can be traced back to the patterns of a certain shrinkage allowance, which are cut on fabric rolls with some different shrinkage allowance.
So, shrinkage grouping for rolls at the lay planning stage should be done properly and allocated to the respective lays. The same information of shrinkage grouping can be used by subsequent processes of garment finishing. This will help in producing consistent garments, by applying the same conditions at finishing processes for the same shrinkage groups.
This in turn helps in reducing the numbers of rejections or deviations from the standard. Hence, if fabric shrinkage grouping is done properly, the cut-to-pack ratio could be improved.
Today, there are several software that individually cater to the different objectives and aspects of the cutting-room such as fabric management. Such fabric management software help in: selection and scheduling of rolls manually, auto-nesting of patterns in CAD software, scheduling jobs to production, tracking production activities and generating reports. There are a few software which enable greater fabric saving through fabric allocation by picking orders for fabric for specific numbers and track the location of the fabric so that the information can be directly sent to the cutting-room.
Although an array of software is present in the market that serve a specific module or a part of it, but Coats Digital’s FastReactFabric is a solution which takes care of all the above points with features like:
- Customised Cut-plan: Generate the most suitable and optimised cut-plan from millions of possible combinations with all the limitations provided in setting and meeting Packing ratios, in one click.
- Work Allocation: Send Cut plan ratio information to CAD team, and laying information to the laying tables on tablet app, with provision of real-time paperless entries on the tab.
- End-bit Management: Plan fabric till the last end-bit easily yet effectively with just a single click of a button. Automatic re-plan suggestion when the number of end-bit increases on the floor.
- Real-Time Reporting: Estimate your fabric requirements accurately. Buy exactly what you need. No more. No less. Least wastage.
- Quality Control: Group similar width, shade, and shrinkage to ensure high standards of quality by preparing relevant patterns, Roll Allocation, Defect tracking and reducing quality rejects, and increase profitability.
- Feedback Mechanism: Master complete control over your factory’s practices by getting real time status and complete tracking.
FastReactFabric is a real-time cutting room planning system infused with advanced intelligence, agile analytics, and mobile technology that is designed specifically to help manufacturers optimise fabric utilisation and reduce fabric wastage.
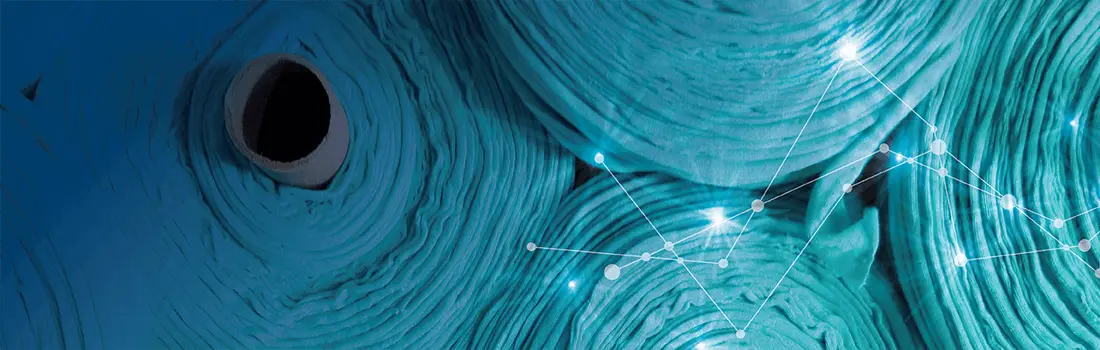
Accelerate your fabric cutting and buying
Learn how you can buy with accuracy and cut with confidence. Talk to an expert today.
Arrange a demo
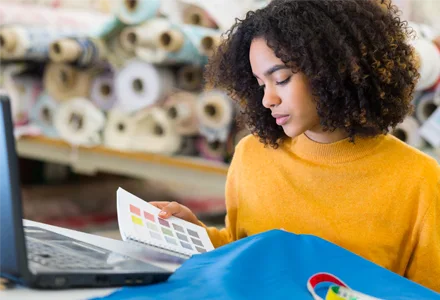
Smart fabric buying: Necessary steps and challenges
All Blog Categories
- Fabric Optimisation
- Corporate
- Design and Develop
- Method Time Cost Optimisation
- Production Planning
- Shop floor execution
- Supply Chain Solutions
- Sustainability
- Videos