GSDCost gives Epyllion transparency of their true cost of production
Epyllion now has the tools to set meaningful production targets based on fact-based capacity data. Additionally, the lost business opportunities, previously caused by over costing or under-costing of orders, were eliminated.
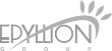
Epyllion Group started its journey back in 1994 as a readymade garments manufacturer and exporter of knit apparel. They are now one of the biggest conglomerates in Bangladesh. They have a diverse portfolio covering knitted garments, textiles, wet processing and garment accessories.
It also has an advanced, vertically integrated garment manufacturing facility, which offers a one-stop service to its customers. The business works with a number of prestigious brands around the world including C&A, M&S, H&M, S.Oliver and Target. The garment division of Epyllion Group includes Epyllion Knitwear Limited and Epyllion Style Limited. Together, they produce 3.8 million garments per month.
22 %
rise in efficiency
5 %
SMV reduction
The challenge
Prior to the installation of GSDCost in 2014, time, cost and capacity calculations at Epyllion were based upon historical time study data created in their own production units. Epyllion acknowledged this data was subjective and outdated. Therefore it was unreliable, with no indication of the real cost of their manufacturing.
As a result, the company lacked visibility and confidence in the true cost of production. Consequently, they were also unable to establish meaningful and realistic production targets for their sewing workers. This lack of transparency had a negative impact on the business. For example, it caused lost revenue by inadvertent under-costing of orders, and an adverse impact on lead times.
Additionally, it was difficult to achieve agreed delivery targets without the extra time and unplanned and costly overtime. Once accurate and reliable SMVs were in place, Epyllion could accurately identify the true cost of production of their operation. As a result, the company could make more informed key business decisions using reliable fact-based data. An additional focus was to optimize and standardize their manufacturing processes to further improve their product quality and production efficiency.
“The need to accurately and objectively quantify the actual standard time of each element of our garment making process was a key requirement for us.”
Shajedur Rahman, COO
Epyllion Group
The objective
The key objective was to establish the common language of GSDCost as the dependable unit of measure for time and cost within their business. Additionally, they aimed to establish the true cost of their production. Subsequently, GSDCost was the catalyst for driving improved cost and production efficiency.
The solution
During the important training and implementation stage, the operational team acquired a thorough understanding of GSDCost. For instance, the training included extensive practical sessions on the shop floor. They were able to create accurate cost benchmarks of their current production. For this reason, this gave the company a crucial awareness of potential excess motions in the methods. As a result, non-value-added activities were eliminated.
“GSDCost has created a significant positive influence upon the challenges we faced. By using accurate data to plan capacity, together with our standardised costing and manufacturing processes, we ensure a smooth production flow.
Shajedur Rahman (Mithu), COO
“The enhanced productivity that has been achieved since using GSDCost directly impacts the bottom line of our business.”
Epyllion Group
Epyllion now has the tools to set meaningful production targets based on fact-based capacity data. Additionally, the lost business opportunities previously caused by over-costing or under-costing of orders, were eliminated. They are also able to understand the true cost of production per style. Consequently, the company was able to make more informed commercial decisions.
“Once we implemented GSDCost, it became apparent that the data previously used for line balancing and capacity planning had been inaccurate and potentially damaging, in terms of late delivery and lost revenue. This situation was unsustainable.”
Golam Mustafa, Assistant General Manager (IE)
Epyllion Group
Why GSDCost?
Shajedur Rahman (Mithu) commented, “We chose GSD as a partner, as they are recognised as the global standard for time and cost in the apparel industry. We were confident that their experience and the proven solution would provide a strong foundation for our company to optimise costs and improve our productivity.”
Related testimonials
Americas
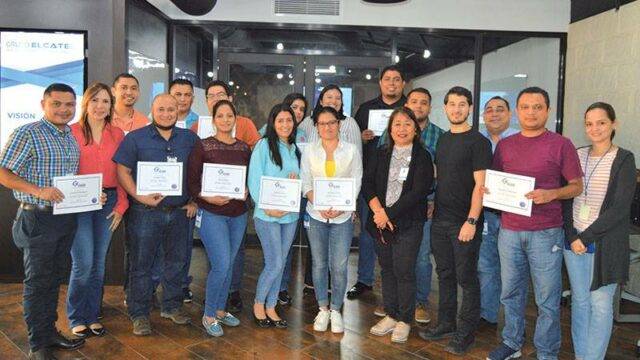
#MethodTimeCostOptimisation
Elcatex Group adopts GSDCost to optimise garment costing
The vertically-integrated manufacturer from Honduras chose GSDCost to quantify and optimise manufacturing methods and garment costing, as a part of…

South East Asia
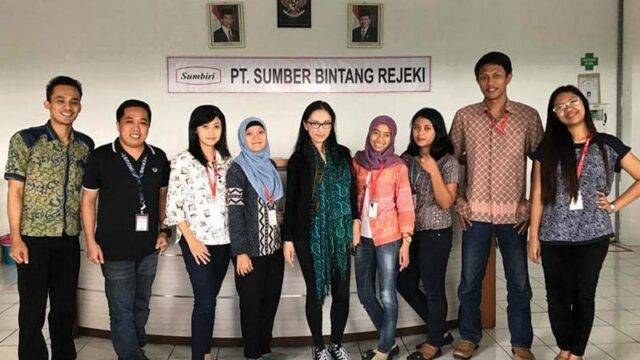
#MethodTimeCostOptimisation
PT. Sumbiri boosts productivity by 13% with GSDCost
The introduction of GSDCost allowed PT. Sumbiri to create accurate method standard for production to help them establish and optimise…
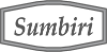