Hoodvian Group automates fabric planning and tracking with FastReactFabric
Hoodvian achieves resounding results with the implementation of FastReactFabric and the group’s continued investment in innovation and digital transformation.
Koggala Garments a member of the Hoodvian Group, selects FastReactFabric to re-engineer their fabric utilisation strategy. They have been operating for the last 30 years and is one the leading garment manufacturers in Sri Lanka.
They’re known for manufacturing a wide range of knitted and woven products such as bodysuits, lingerie, nightwear, and knitted tops for brands such as Next, Sainsbury’s, George, Tesco, Lidl, Carole Hochman, Gap, Matalan and David’s Bridal.
2 %
Saving on fabric consumption
70 %
Fabric cutting room automation
The Challenges
1. Inefficient fabric tracking process
The diligent team at Hoodvian found it hard to keep a complete track of the fabric used on the cutting floor and the fabric returned back to the warehouse, using manual spreadsheets. The team wanted a digital solution that could help them effectively track fabric, from the warehouse to the cutting floor.
Solution: Automated fabric tracking
The Cut module of FastReactFabric (formerly IntelloCut) tracks every inch of the fabric used on the cutting floor and auto-reconciles the fabric data in reports that can be generated instantaneously in a single click. Reports such as ‘Aggregated Reconciliation Report’ and ‘Roll Usage Report’ give the visibility of the fabric performance in terms of consumption and wastage, and keep a track of total fabric used on the cutting floor and returned to the fabric warehouse.
“With a team that was truly committed to the system’s implementation, execution and follow up, we had a firm belief that FastReactFabric could deliver great results for us.”
Nilantha Ratnayake, CEO
Koggala Garments
2. Increased end-bits on the fabric cutting floor
With increased production orders on the floor, the generation of end-bits (an end-bit is a piece of fabric that is left after a roll is used for spreading) also increased, which made the end-bit management process difficult for the factory team.
Solution: Efficient end-bit tracking and usage
With FastReactFabric’s data feedback mechanism, the Hoodvian team can now keep a real-time track of the end-bits generated on the cutting floor. This allows the team to modify the cutting plan as per the actual number of end-bits. All the end-bits are tagged, bundled and kept style-wise for easy procurement.
The team also implemented the process of splicing, which ensured that all the generated end-bits are utilised within the same lay, providing the maximum end-bit utilisation. With continuous improvement in end-bit utilisation, the factory team was able to save 2% on the overall fabric consumption.
3. Manual processes leading to increased effort and time
The Hoodvian team needed a digital solution that could help them in saving effort and time spent in the current processes. The manual processes of fabric planning and execution led to errors which ultimately resulted in further lost time and effort.
Solution: Automated planning and execution
FastReactFabric’s advanced cut plan and seamless end to end execution helped the factory team in having full control over the set processes. The automated planning and real-time visibility of data helped the team to identify, and eventually, reduce errors. Manually filled lay slips were replaced by system-generated digital lay slips which reduced the team’s manual effort and saved time. Consequently, the factory team was able to automate 70% of their fabric buying and cutting room processes.
“The use of FastReactFabric delivered unprecedented results that amazed everyone and added further commitment across the board to probe aggressively what other opportunities exist to bring in more positive results.”
Nilantha Ratnayake, CEO
Koggala Garments
4. Disconnected inter-department information flow
There were unnecessary delays caused in the fabric cutting execution due to gaps in the information flow across the factory. The factory team required a digital system that ensured a quick and smooth flow of information across departments for efficient and timely execution of processes.
Solution: Seamless inter-department communication through FastReactFabric reports
FastReactFabric has provided numerous reports, catering to a variety of information, as per a department’s need. For example, the “Lay Plan Report” is used by the factory team to communicate the marker information within the cutting and CAD department, improving the communication flow between the two departments.
The FastReactFabric team trained a project lead in the factory whose responsibility is to keep a check and help the factory team on all the set processes. This has helped the factory in ensuring efficient usage of the FastReactFabric system and gain significant improvements.
Related testimonials
South Asia
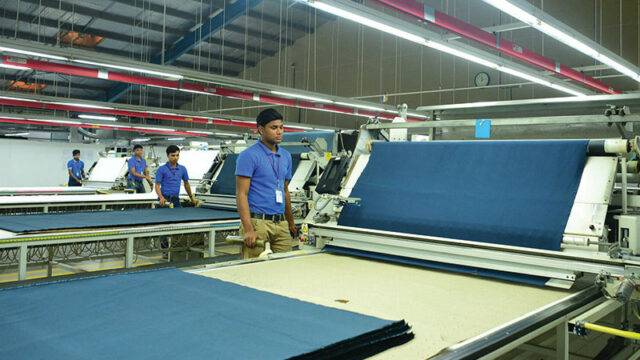
#FabricOptimisation
Univogue Group boosts fabric utilisation by 2% with FastReactFabric
The innovative apparel supplier is committed to continuously learning and developing, and investing both human and financial capital, to stay…
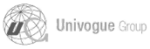
South Asia
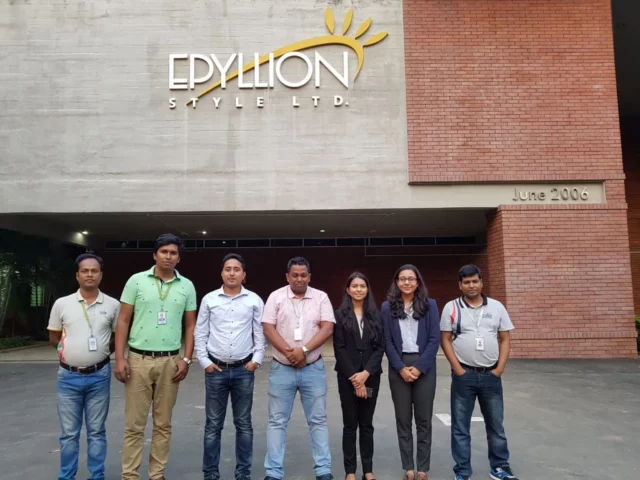
#FabricOptimisation
Epyllion Group reduces fabric buying cost by 2% with FastReactFabric
Using FastReactFabric Epyllion automated 70% of their fabric booking processes, enabled informed decision making and provided advanced business intelligence
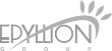
South East Asia
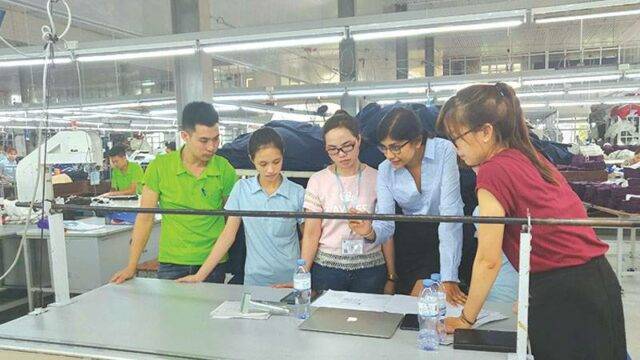
#FabricOptimisation
FastReactFabric helps Song Hong to reduce 60% of fabric planning time
FastReactFabric accounts all the wastages on the cutting floor and reconciles the data in the reports for any desired date…
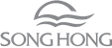