Nobland International improves productivity by 13% with GSDCost
GSDCost has enabled Nobland to set realistic production goals based on accurate SMVs, resulting in increased productivity and seamless CM negotiations between sales teams and factories.

About the customer:
Headquartered in Seoul, Republic of Korea, Nobland was founded in 1994, and started out as a key production partner for New York designer brands requiring quality knitted and woven clothing products.
The company has grown rapidly since and is now a leading global apparel production company with more than 15,000 employees, two production bases in Indonesia and Vietnam and a design centre in New York. The company boasts an annual turnover of almost $410 Million and produces over 9 million pieces per month.Its customers include: GAP Inc., Target, JCPenney, Kohl’s, Walmart and Levi’s, among many others. Nobland operates on an advanced full-service vendor model that can scale effectively from the design and production of intricate designer fashion items to large scale orders for global retail enterprises.
The Challenge – Inaccurate capacity plans led to time-consuming CM negotiations
A lack of a scientifically based method-time-cost standard proved highly restrictive to achieving accurate production goals and appropriate CM price calculations.
With capacity plans founded entirely on historical data based on the planning administrator’s experience, and with production goals set on subjective break-even points, Nobland lacked the consistency and uniformity it needed to set realistic production goals or a realistic production flow for its sewing lines.
Its subsequent difficulty in establishing accurate CM cost plans additionally resulted in lengthy negotiations between sales teams and factory managers regarding both production targets and employee wage agreements.
GSDCost Training
Following the adoption of GSDCost, Nobland International undertook a rigorous three-month GSDCost training bootcamp so that relevant Nobland teams could gain a good theoretical understanding of GSDCost motion codes and standard core style sequences. The solid experience with hands-on training of the software solution, enabled Nobland to gradually establish its own robust Standard-Minute library for its core garment styles.
“We were able to familarise ourselves with the GSDCost scientific concept reasonably quickly across several training sessions with Coats Digital’s experts. The numerous sessions enabled all team members to get up to speed with the desired training levels very fast, so that a more accurate process analysis could be achieved. This factor has enabled us to provide reliable SMV targets for the benefit of our sales and production teams, and we are now using our GSDCost knowledge as well as sharing new ideas, so we can continue to build a successful library for our core styles.”
Don Choi, IE Team Manager,
Nobland International Inc
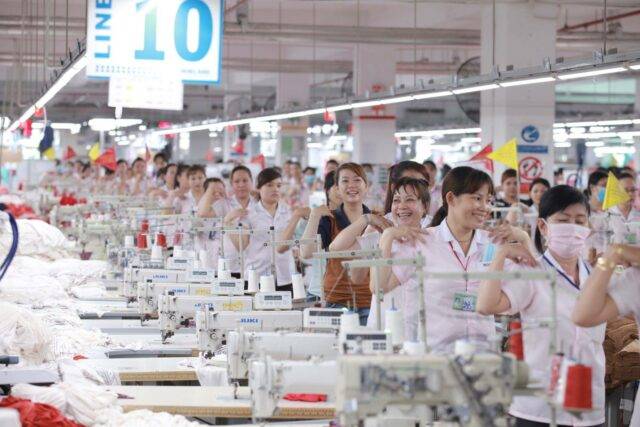
The Solution
Nobland’s teams successfully completed the Phase-1 and Phase-2 GSDCost certification training programme, in August 2022, and were able to effectively use the scientifically obtained SMVs to provide accurate costing, planning and production targets.
As a result of the training and GSDCost implementation, Nobland not only realised a significant overall efficiency improvement of 13% across its sewing lines, but also eliminated unnecessary disagreements between sales and factory floor teams regarding CM costs and processes.
Its management team has additionally been able to set realistic achievement rates for employees based on achievable targets.
Coats Digital’s GSDCost method analysis and pre-determined times solution is widely acknowledged as the de-facto international standard across the sewn products industry. The solution supports a more collaborative, transparent and sustainable supply chain, in which brands and manufacturers establish and optimise ‘International Standard Time Benchmarks’ using standard motion codes and predetermined times. This use of a common language and standards supports accurate cost prediction, fact-based negotiation, and a more efficient garment manufacturing process, while concurrently delivering on CSR commitments.
“We are delighted that Nobland has achieved such remarkable results following its adoption of GSDCost. Intensifying, global price competition and increasing demands for faster deliveries and more varied style assortments has meant that fashion manufactures must remain innovative, agile and most importantly, digitally-focussed, if they want to successfully navigate a highly volatile trading environment. By standardising SMVs according to scientific principles, apparel manufacturers can ensure they are one step ahead by increasing production efficiencies quickly and making deals with buyers based on factually correct costs. Nobland’s dedication to the GSDCost training programme was second to none and it’s teams can be exceptionally proud of what they have achieved. Nobland is consequently leading the field with regards its knowledge and utilisation of GSDCost, and it remains one of the most agile and competitive players in our territory as a result.”
Irene Won, Customer Success Manager,
Coats Digital
“Coats Digital’s GSDCost is the only solution available that uses scientifically-proven methods to assess production goals realistically, so that accurate planning can be obtained and increased productivity achieved. GSDCost’s code generation analyses for various production tasks provide us with rigorous, consistent data insights that make production improvement activities possible. Based on detailed motion behaviour analyses of the most efficient production processes, we have been able to train production operators effectively and set standards that work. We are delighted to have realised a 13% efficiency improvement so quickly and our realistic benchmarks have made each of our factories much more competitive as a result.”
Eunice Kim, Executive Director of Customer Solutions Planning,
Nobland International Inc.