Azim Group increases planning efficiency by 15%
Benefits realised include higher efficiency in order confirmation time, performance to plan, cut to ship, plan & actual factory efficiencies and report generation time.
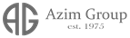
Established in 1975, Azim Group is a pioneer of the Bangladesh Garment Industry. Azim Group produces garments for leading brands in the United States, Europe, Asia and South America. Its clients include CK Jeans, Berksha, Walmart, Kohl’s, Perry Ellis, Elcorte Ingles, Lands’s End, and Falabella.
Azim Group is committed to becoming a role model for environmental and social responsibility and is actively engaged with global programmes such as: the ZDHC, The Higg Index and Amfori BEPI to promote the highest sustainability standards. Azim Group factories are certified by Global Organic Textile Standard (GOTS), Organic Content Standard (OCS) and OEKO-TEX Standard 100.
15 %
improvement in Plan vs Actual efficiency
7 %
factory efficiency improvement
68 %
reduction in report generating time
97 %
faster order confirmation
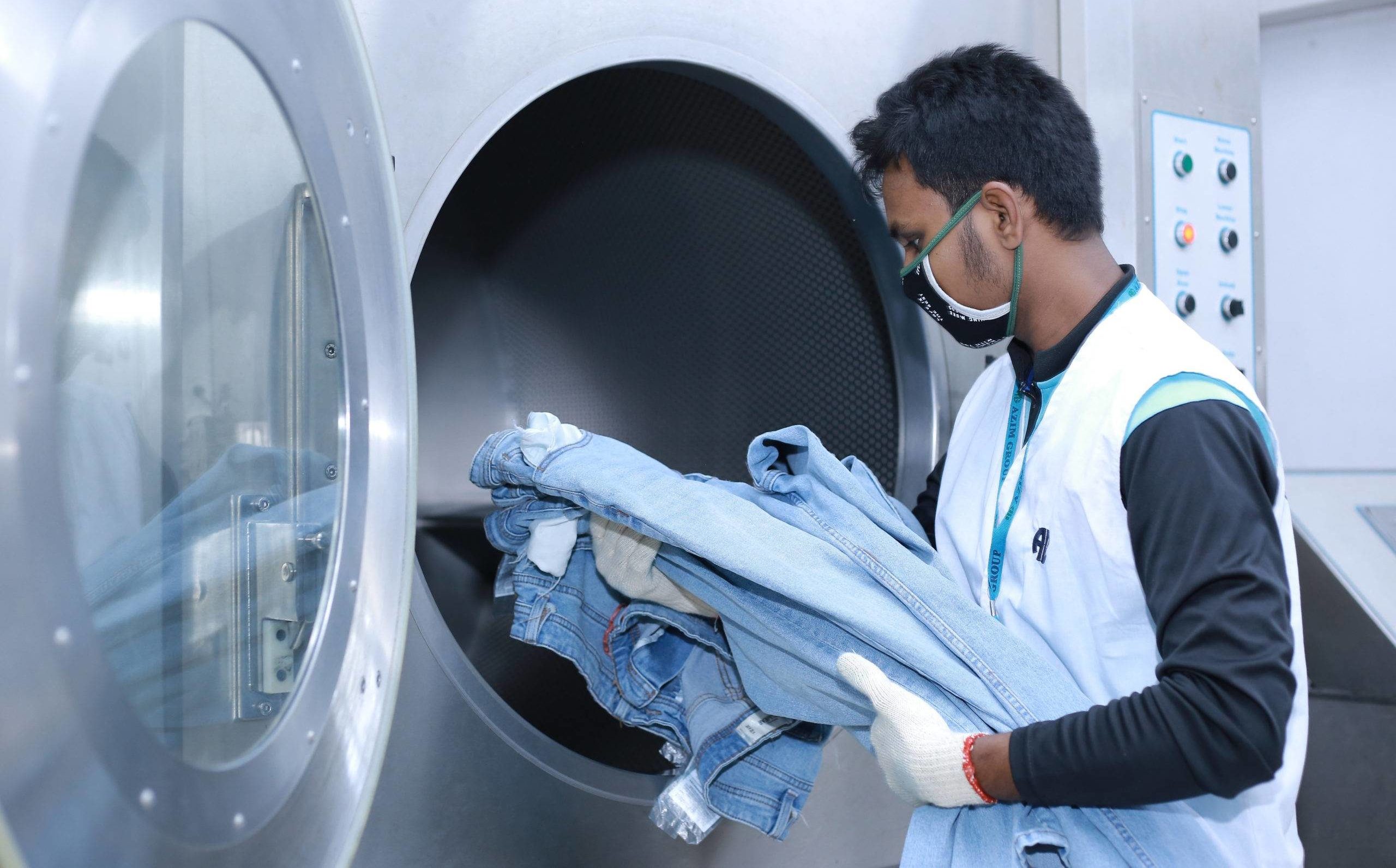
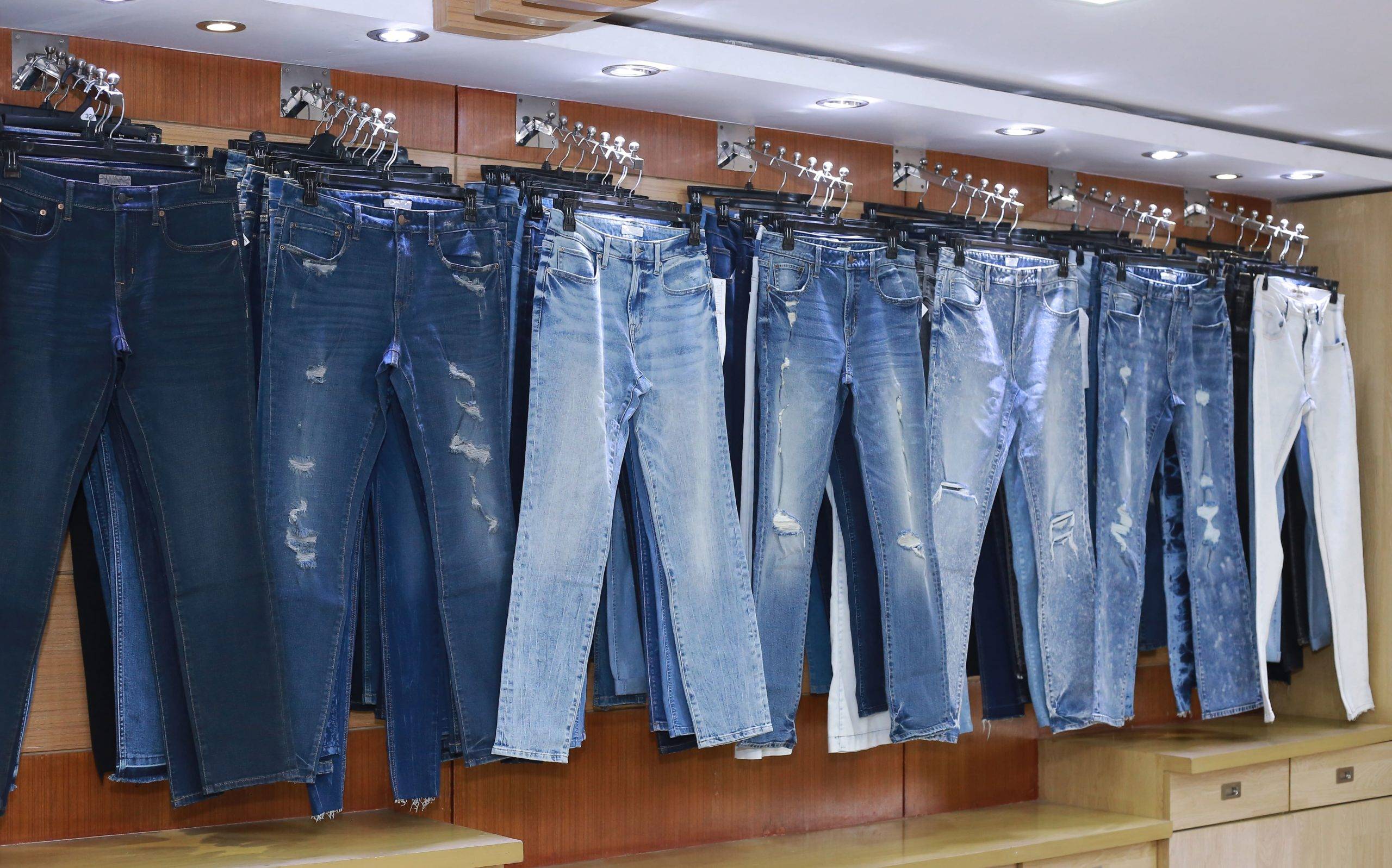
Challenges and their solutions
1. Disconnected order tracking and reporting in Excel spreadsheets meant issues resulting in lost business
Prior to implementing FastReactPlan, capacity management and line planning teams lacked the pinpoint accuracy required to respond to the buyer’s latest changes. As a result, additional effort and regular reviews were needed with merchandising to ensure all teams had a unified approach to delivery.
With important information siloed in multiple sources across email, Excel spreadsheets and over phone conversations, manual planning processes proved time-consuming and lacked efficiency. Based on insufficient data, capacity was often overbooked or under-booked, causing late deliveries and the unnecessary rejection of new orders.
Solution
Following the implementation of Coats Digital’s FastReactPlan, Azim Group has all relevant information available in one platform, ensuring comprehensive data transparency and visibility across merchandising and planning processes, so that teams can update and respond to new information in an agile way.
Now that minutes-based load vs capacity monitoring has also been accurately established on true actual line plans, merchandising and planning teams can establish accurate plan-based capacity reports within minutes, guaranteeing a realistic capacity status, with timely warning alerts, to avoid overbooking or under-booking scenarios. As a result of the FastReactPlan implementation, Azim Group has realised a 15% increase in planning efficiencies; And a 97% faster turnaround in order confirmation, with orders being confirmed in just 30 minutes instead of two days.
“Since the implementation of FastReactPlan, it was crucial that we saw consistent improvements in our planning process. I am pleased to say that we were successful in achieving this. In the first year, our planning efficiency increased by 15% and will continue to increase going forward. Furthermore, the new system has helped streamline key processes such as order confirmation, capacity forecasting and line allocation – providing more accurate results compared with previous methods. Ultimately, the increased efficiency is reflected in higher growth in our business.”
Mr. Ehsan Islam,
Operations Manager at Azim Group
“Following the implementation of FastReactPlan, we started seeing positive results quickly. These are improvements across major KPI parameters including factory efficiency, planning efficiency, on-time-delivery, and on-time T&A completion. Moreover, the new system is able to process data much faster than the tools traditionally used in the RMG industry. Thus, it enables management to make more informed, data-driven strategic and financial decisions.”
Mr Farhan Azim,
Deputy Managing Director, Azim Group
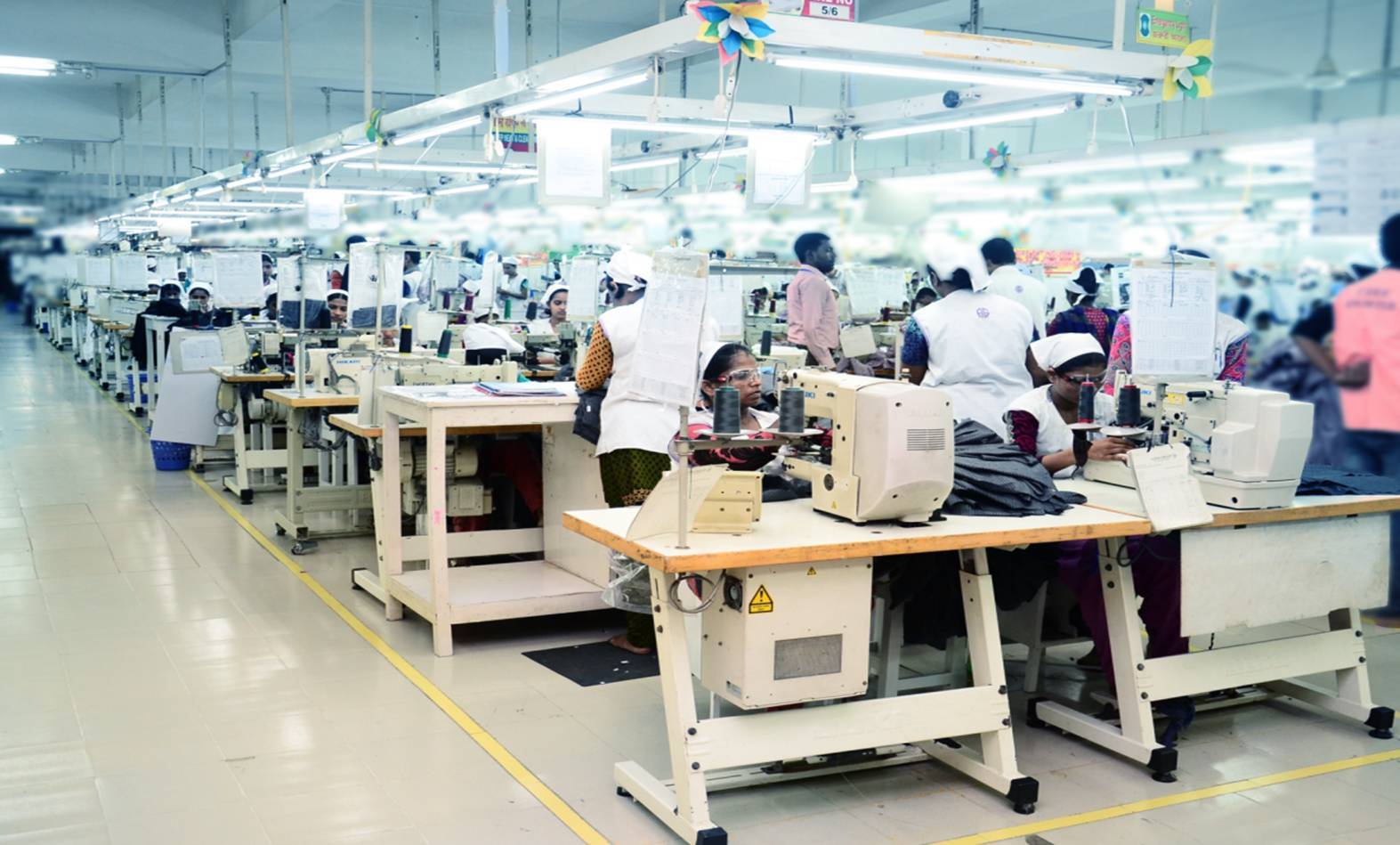
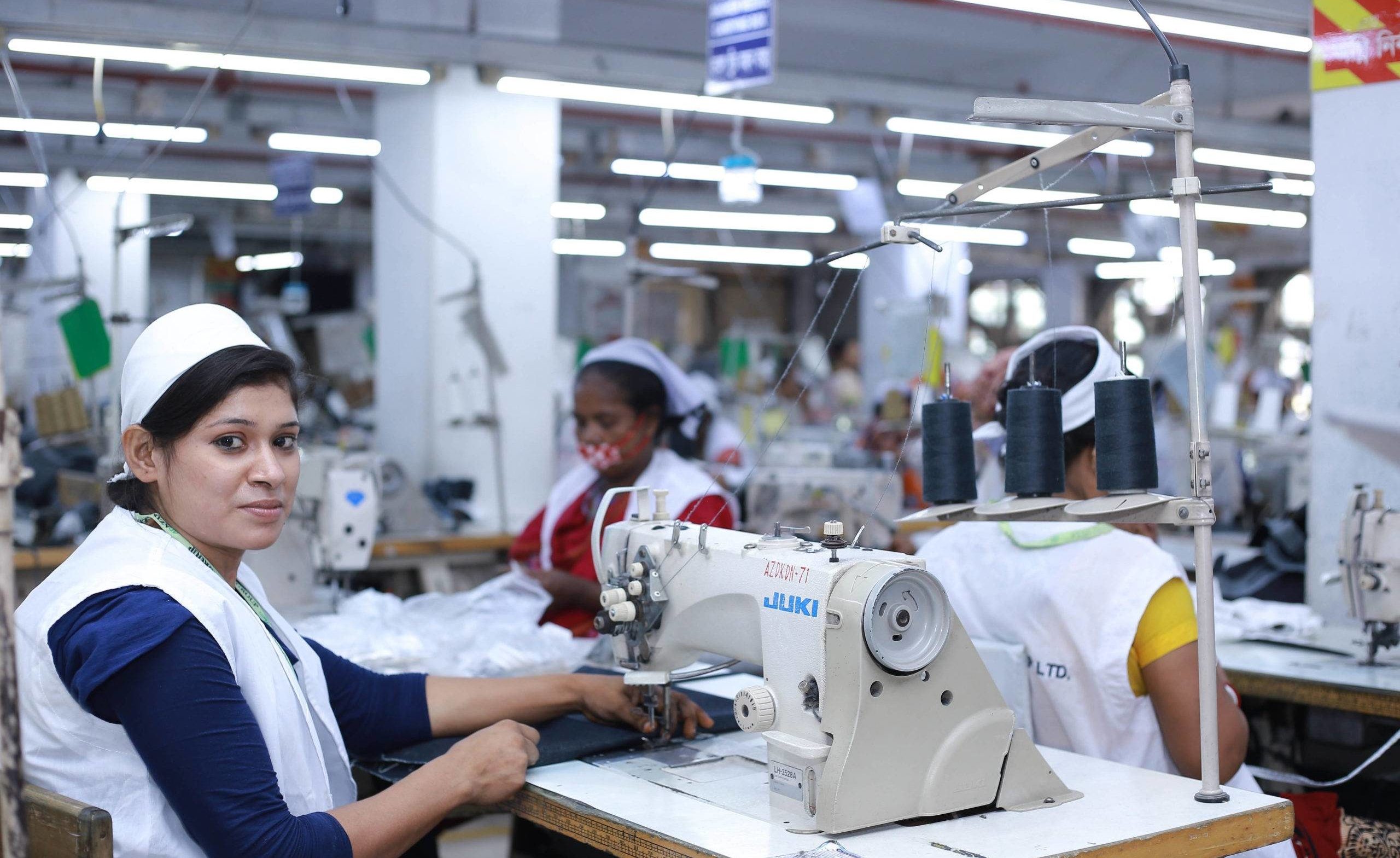
2. Data in multiple sources and limited visibility of forward load capacity meant order confirmations were delayed, lead-time projections were not fully accurate and business decisions were based on insufficient data
With production plans made mostly at the style or even the PO level, a series of time-consuming drill-down meetings were often required to iron-out potential problems and ascertain the fastest remedy. Re-plan changes were consequently difficult to apply quickly, resulting in late deliveries and confusion with regards Work in Progress (WIP) reporting and Time & Action (T&A) prioritisation.
Target setting using average efficiency assumptions, not only lead to inaccurate capacity forecasting, but also unrealistic delivery projections and the inability to respond to customer demands for quicker order confirmation.
Solution
Since implementing FastReactPlan, standardised PO, colour and delivery level visibility is now available across all departments, establishing one version of the truth throughout the business and a single source of all information for better-informed decision making. All departments are now using FastReactPlan to create accurate, real-time reports and daily activity priorities, including KPIs, all of which are readily available for all departments to see. As a result, Azim Group has saved nearly six Person Days per month in time efficiencies – a 68% timesaving in report generation.
Realistic plan targets, factoring in robust efficiency targets by product type, learning curve requirements and the production line’s performance have also helped to significantly increase efficiency and reduce last-minute firefighting. Factory efficiency has consequently increased by 7%; whilst Cut to Order, Ship to Order and Cut to Ship efficiencies have also increased by 0.37%, 0.89% and 1.36%, respectively.
“The FastReactPlan team understood the technological gap we previously faced in our planning process and were successful in providing us with required solutions. The end result is a customisable and visual system which is easy to operate for non-technical individuals. The system takes real-time data and is able to auto-generate many key reports, hence saving person hours and increasing overall efficiency of all concerned departments.”
Mr. Istiak Mohammad Rana,
Manager – IT & Communications, Azim Group
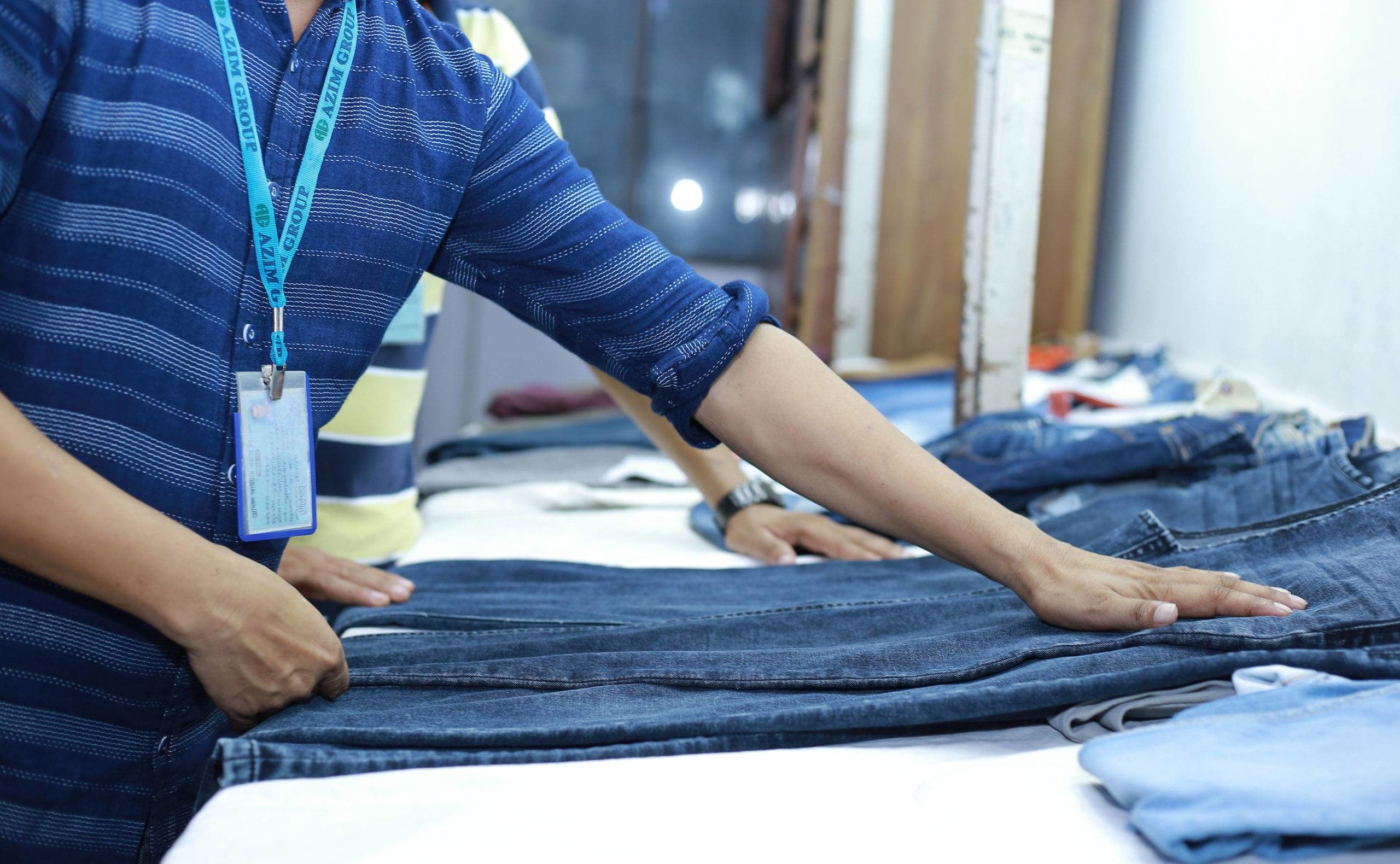
“Azim Group project teams were very cooperative from the very beginning of the project. Their dedication, actively achieving deadline, exploring mindset to achieve more from FastReactPlan helped to complete the project within six months and they are now getting the benefits of the digital transformation of planning processes through the Coats Digital product.”
Ashraful Alam Chowdhury,
Senior Implementation Consultant, Coats Digital
FastReactPlan is developed exclusively for the fashion, textile and apparel industry and can be configured in multiple ways to reflect industry best practice and specific business requirements. The Azim Group project will include detailed planning of the sewing lines as well as the scheduling of cutting, laundry and finishing processes within its denim specialised subsidiary, Global Outerwear Ltd, using the highly visual, sophisticated tools of the FastReactPlan planning board.
To download this case study as a PDF, please click the button below:
Related testimonials
South Asia
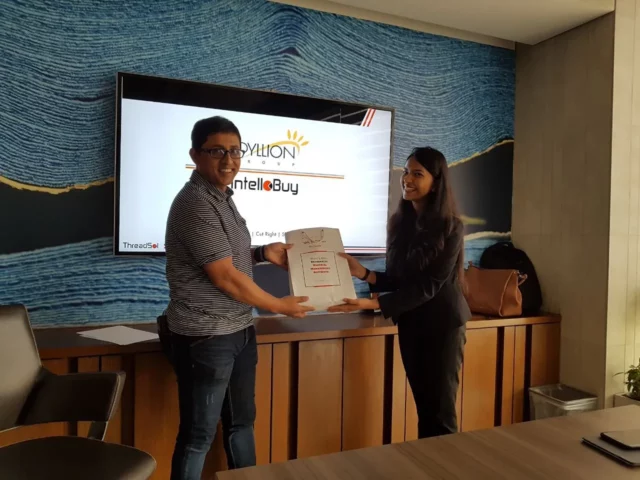
#ProductionPlanning
Epyllion increases delivery performance by 58% with FastReactPlan
The use of the integrated Critical Path management tools and the high-level control tower view for management and marketing teams…
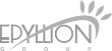
South East Asia
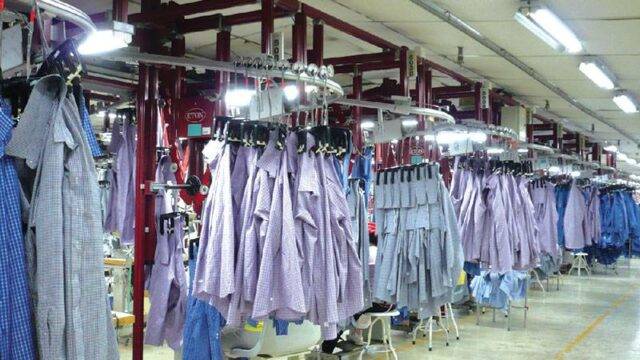
#ProductionPlanning
Esquel Group adopts FastReactPlan to support growth plan
Esquel Group turned to Coats Digital in order to centralise its capacity management and production planning capabilities across its manufacturing…

South Asia
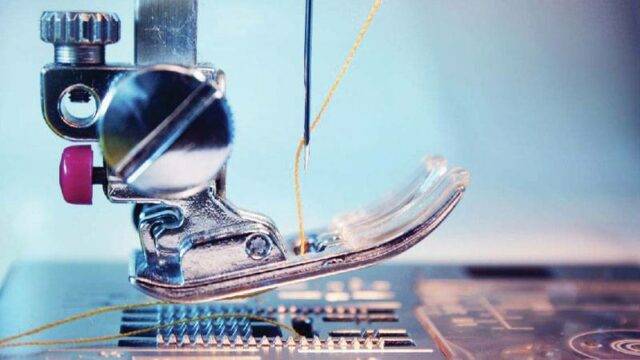
#ProductionPlanning
MAS Active achieve substantial performance improvements with FastReactPlan
The top sportswear supplier dramatically improved performance to plan, increased factory productivity and enhanced customer service
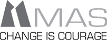