Univogue Group boosts fabric utilisation by 2% with FastReactFabric
The innovative apparel supplier is committed to continuously learning and developing, and investing both human and financial capital, to stay attuned to evolving industry trends and technology.
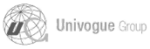
The Univogue Garments Company Limited is one of the leading garment manufacturing companies in the Chittagong Export Processing Zone, Bangladesh.
Univogue manufacturers a wide range of woven and knitted apparel for men, women and children, and caters to leading brands such as Target, Levi’s, Haggar, Perry Elis and Li & Fung.
82 %
Reduction in fabric planning time
2 %
Increase in fabric utilisation
The Challenges
1. Lack of process automation
With manual processes and the lack of automation, it became hectic for the Univogue team to manage the planning and execution of multiple orders at a time. Additionally, the complexity of the products Univogue manufactures and the materials it uses, resulted in a lot of extra manual effort while planning the orders. Since all the processes, starting from cut plan creation and fabric grouping to assigning the groups to markers/lays, were done manually, optimum results could not be assured every time.
As a consequence, the Univogue team aimed to automate all processes in the cutting room, from planning to execution, to save time and effort.
Solution
FastReactFabric’s (formerly IntelloCut) advanced technology plan module helps the team to get an optimum plan with just one click. The system also helps the team in accurate fabric grouping as per the user’s requirements, and to assign the fabric groups to the markers/lays, ensuring maximum fabric utilisation. With the help of FastReactFabric, Univogue was able to reduce their cutting room planning and execution time by 82%.
2. Manual handling of numbering and bundling data
The process of numbering and bundling on the cutting floor is essential to ensure that the quality of the garments is not compromised. The Univogue team would collect lay slips from the cutting floor to create roll-wise numbering and bundling report, by manually entering data in the excel spreadsheets. This process was not only time-consuming but also prone to multiple errors.
Solution
FastReactFabric floor feedback mechanism helps to populate the data of each lay into reports as soon as the lay is completed. The data of all the rolls being used is updated in the system in real-time which makes it really easy to generate numbering and bundling reports.
3. Improper utilisation of end-bits generated on the cutting floor
The end-bits can only be utilised if they are managed properly in a structured way. Inside the factory, the end-bits left behind were used only for a panel replacement activity. There was a designated space to keep the end-bits, however, this space was not managed properly, resulting in the mix-up of end-bits of multiple styles. This gave rise to a lot of confusion, resulting in poor visibility of fabric on the floor and the end-bits getting wasted.
Solution
FastReactFabric not only provides the visibility of available end-bits to the factory but also plans them in smaller markers to ensure their effective utilisation. The Coats Digital team also helped Univogue to establish a structured end-bit management system during the implementation. All the end-bits are now measured, tagged and then stored at a designated place which helps the team to identify the end-bits easily.
4. Inefficient wastage tracking and segregation
In order to reduce wastage, it is important to have clarity on the type of wastages occurring on the cutting floor. The team at Univogue wanted to identify the avoidable and unavoidable wastages on the cutting floor.
Solution
FastReactFabric has helped in providing a complete wastage breakdown to the factory. The team can now download order-wise reports to see the wastage breakdown in seven categories which is also segregated on the basis of customer, style, fabric and date. This information has enabled the team to take measures to reduce avoidable wastage, resulting in an increase in fabric utilisation by 2%.
“FastReactFabric helped us to manage fabrics with different characteristics in a very efficient manner, with clear traceability in the cutting process. FastReactFabric’s contribution towards maximising fabric utilisation was one of the main contributory factors for Univogue to become competitive in the industry.”
Jagath Priyantha, Director
Univogue Garments Company Limited
5. Lack of visibility and access to real-time data
The entire on-floor data entry was done manually, including lay slip entry and recording of fabric excess/shortage. This data was then entered into excel spreadsheets, which made data reconciliation a difficult and time-consuming process.
Solution
FastReactFabric’s tablet application allows the on-floor team to make real-time entries, which makes it easier for the planning team to view the latest information, such as current achieved consumption, cut quantity and other relevant details. This information can then be used to make business-critical decisions.
6. Improper accountability of fabric used in panel replacement
Since fabric amounts to 50%-70% of the total garment cost, it is important for any factory to keep track of the areas where the fabric is being used. The team at Univogue used to keep a record of panel replacement in terms of the number of times it occurred in one order and not the actual amount of fabric used in the process.
Solution
The panel replacement team is now equipped with the FastReactFabric’s tablet application which tracks every inch of fabric being used in panel replacement for an order. The tablet application provides detailed information, including whether it was used from an end-bit or from a fabric roll.
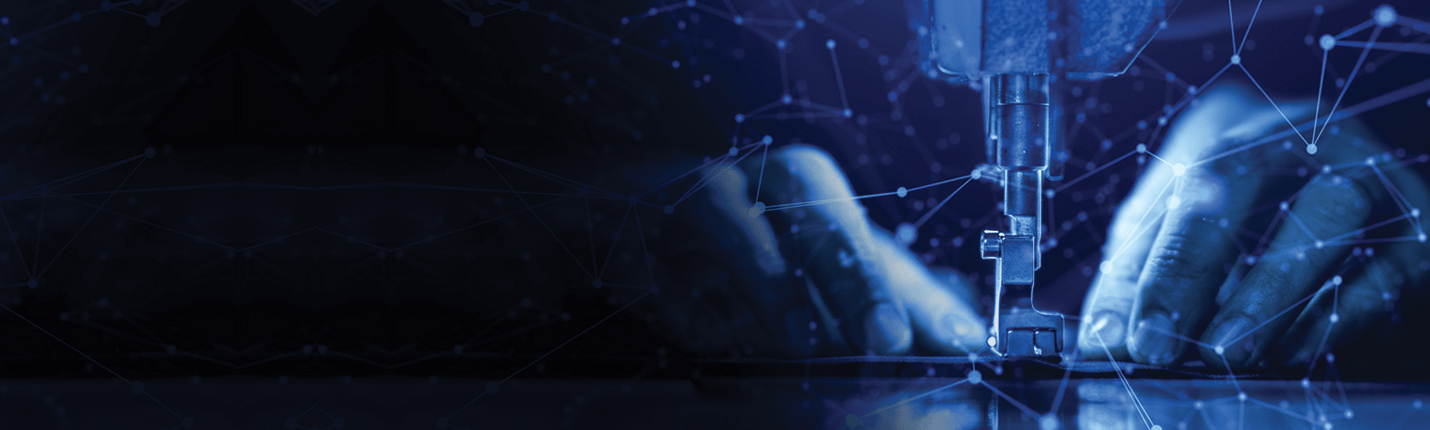
Smart Fabric Planning with FastReactFabric
Stop wasting fabric and start increasing profit. Buy fabric with accuracy and cut with confidence.
Related testimonials
South Asia
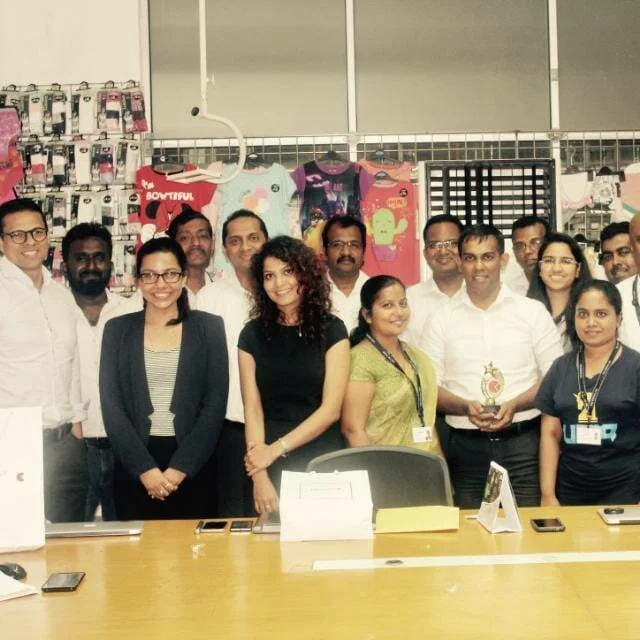
#FabricOptimisation
Hoodvian Group automates fabric planning and tracking with FastReactFabric
Hoodvian achieves resounding results with the implementation of FastReactFabric and the group’s continued investment in innovation and digital transformation.
South East Asia

#FabricOptimisation
GJM (Luenthai) cuts fabric wastage to boost its top-line with FastReactFabric
GJM improves their processes to generate real-time optimised plans, fabric tracking and reports with the objective of boosting performance and…
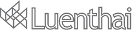
South East Asia
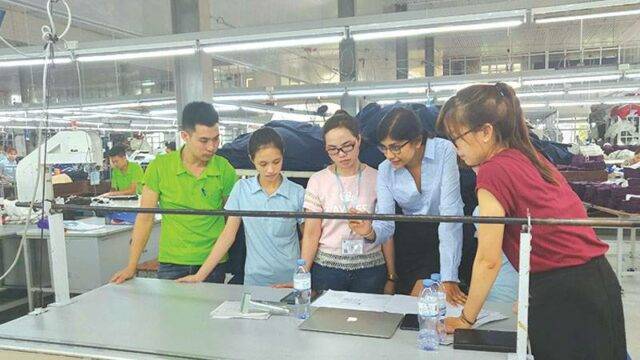
#FabricOptimisation
FastReactFabric helps Song Hong to reduce 60% of fabric planning time
FastReactFabric accounts all the wastages on the cutting floor and reconciles the data in the reports for any desired date…
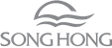