FastReactFabric helps Crystal Martin plan their fabric cutting efficiently & reduce fabric wastage.
FastReactFabric's advanced cut-plan, automation of cutting execution and integration with the factory’s ERP system - AX Dynamics, helped the factory team to reduce their planning time by 40%.

Crystal Martin International Group selects FastReactFabric to automate and optimise their fabric cutting.
The Crystal Martin International group was formed in Hong Kong in 1970, in a small workshop with a few sewing machines and knitting looms, producing sweaters. The group has grown from strength to strength and today has 20 self-operating manufacturing facilities spread across 5 countries.
With a workforce of approximately 80,000, Crystal Martin delivers over 470 million pieces of apparel in a year to top apparel brands around the world. Their broad range of apparel products include lifestyle wear, denim, intimate wear, sweaters, sportswear and outdoor apparel.
40 %
Reduction in planning time
The challenges
1. Lack of automation of processes
With manual fabric planning and spreadsheet-based communication across departments, it was difficult for the Crystal Martin team to expedite their cutting operations. Crystal Martin needed a solution that could replace the existing manual methods of fabric planning and execution with automation, to reduce time and effort.
Solution:
The Cut module of FastReactFabric (formerly IntelloCut) generates a cutting plan for a production order within a few clicks. Its end-to-end execution control gives the factory a complete status of the ongoing processes in real-time. In the case of Crystal Martin, the system’s advanced cut-plan, automation of cutting execution and integration with the factory’s ERP system, AX Dynamics, helped the factory team to reduce their planning time by 40%. The automated planning and real-time fabric data visibility helps the team to identify and reduce recurring errors.
2. Inefficient fabric Utilisation
The team at Crystal Martin wanted to improve their fabric utilisation. As more than half of their total garments’ cost consisted of fabric, poor fabric utilisation resulted in an uneconomic cutting environment and reduced profits for the manufacturing facility.
Solution:
FastReactFabric’s fabric grouping feature allows the factory to group the fabric rolls based on different widths, ensuring the least wastage along the width of the fabric, ultimately leading to maximum fabric utilisation. With the system’s assistance and continuous improvement in the cutting room processes, the factory was able to improve the overall fabric utilisation.
“The team’s ability to grasp things quickly and conceptually understanding the processes led to quick implementation of FastReactFabric and sustainable improvement in their everyday tasks.”
Jaya Choudhary, Professional Services Manager,
Coats Digital
3. Improper material management and control, and manual reporting
The management team at Crystal Martin faced numerous challenges affecting fabric management, such as issues related to end-bit management, fabric tracking and proper information flow across departments. Additionally, manual reconciliation of data and report-making consumed a lot of factory’s time and effort which made it difficult to make business-critical decisions on time.
Solution: Real-time fabric tracking and visibility, as well as accurate reporting
FastReactFabric helps the planning team to make real-time decisions with the help of live production statuses and a continuous floor feedback mechanism. The fact that FastReactFabric can record every inch of fabric used on the cutting floor, allows the factory team to gain end-to-end visibility over the cutting operations. FastReactFabric also helps reconciliate a variety of cutting room data into organised order-wise and style-wise intuitive reports that can be accessed at any time with a single click, allowing the factory to make informed decisions on time.
“The sheer determination and dedication of the Crystal Martin team in learning the software acted as a positive catalyst to the implementation process. The smooth coordination and understanding between various departments of Crystal Martin was a big reason for the project to be successful.”
Jaya Choudhary, Professional Services Manager,
Coats Digital
Related testimonials
South Asia
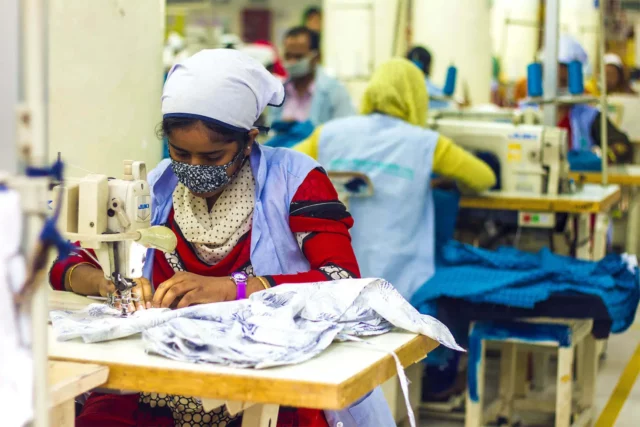
#FabricOptimisation
Dekko Designs Ltd. gains 1% top-line growth with FastReactFabric
Bangladesh’s leading garment manufacturer Dekko Designs Ltd. chose Coats Digital’s FastReactFabric to implement best practice fabric planning and cutting execution…

South Asia
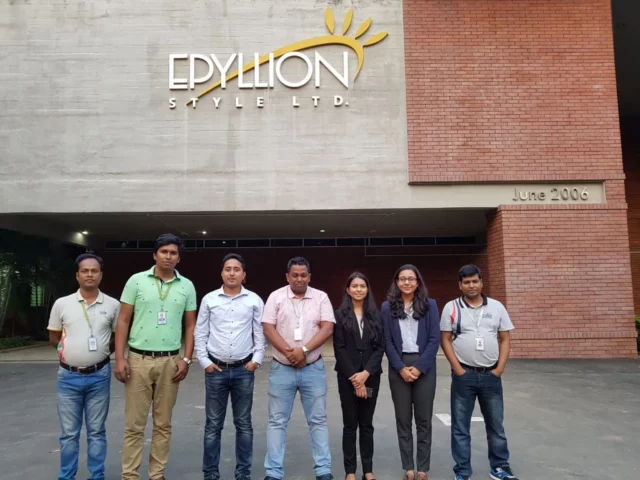
#FabricOptimisation
Epyllion Group reduces fabric buying cost by 2% with FastReactFabric
Using FastReactFabric Epyllion automated 70% of their fabric booking processes, enabled informed decision making and provided advanced business intelligence
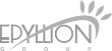
South East Asia

#FabricOptimisation
GJM (Luenthai) cuts fabric wastage to boost its top-line with FastReactFabric
GJM improves their processes to generate real-time optimised plans, fabric tracking and reports with the objective of boosting performance and…
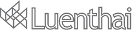
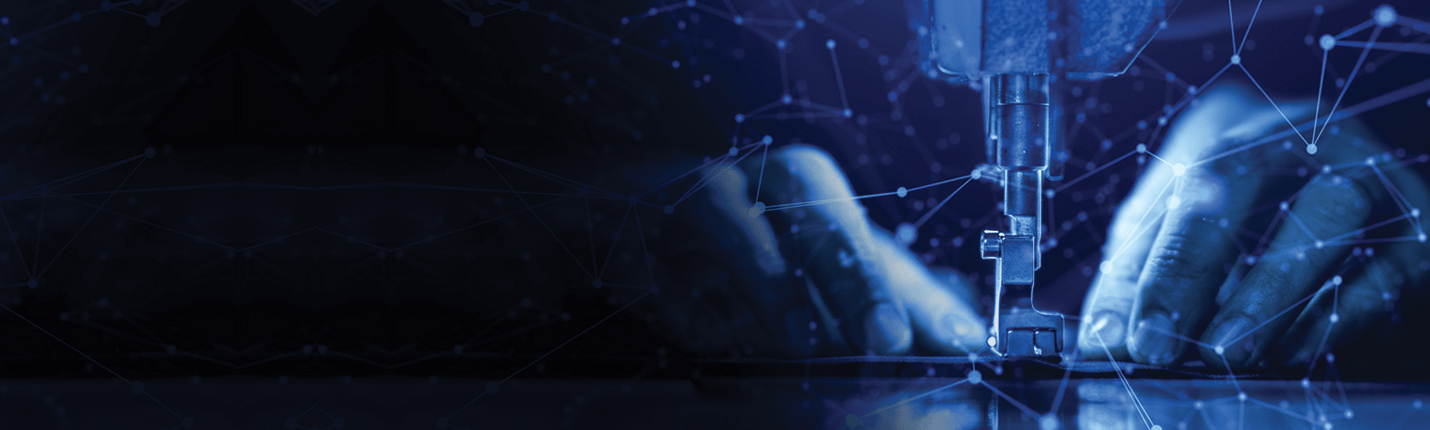
Smart Fabric Planning with FastReactFabric
Stop wasting fabric and start increasing profit. Buy fabric with accuracy and cut with confidence.