Tata increase delivery performance by adopting FastReactPlan
FastReactPlan was selected to give increased visibility of both the production process and the pre-production critical path events. The system has ensured that there is clear visibility of order status.

Established in 1985, Tata has grown to be one of the largest belt manufacturers in the world today. Based in Guatemala, they have an annual capacity of over 8 million units per year. Tata produce all types of belts and have a global customer base that includes Levi’s, Dickies, Target, Fossil and Relic brands plus many wholesale clients.
In addition to the high capacity factory, allowing them to produce very large numbers of high-quality leather belts, Tata’s growth can also be attributed to their convenient geographical location, a highly educated and trained workforce, quick, duty-free deliveries, combined with a very forward-thinking attitude and willingness to invest in new ideas and technologies.
$ 100000
Work in progress reduced in 6 months
20 %
Reduction in workforce
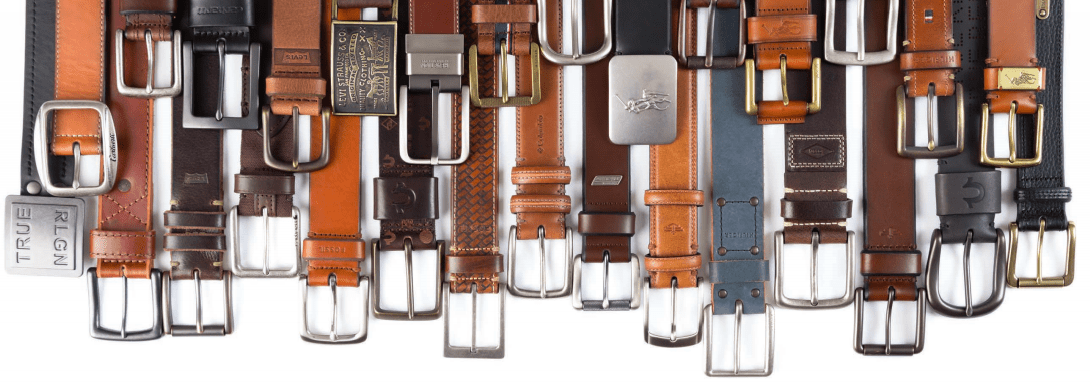
The Challenges
Having invested significantly in state of the art Italian machinery, Tata had also implemented an ERP system followed by the introduction of lean manufacturing principles within the business. However, with the company continuing to grow and competition continuing to increase, Tata were keen to improve efficiency even further by gaining clearer visibility of the entire production process. Tata undertook extensive market research to find a solutions provider that could provide the functionality they required whilst offering extensive industry knowledge and experience.
The Solution
The FastReactPlan planning system was selected to give increased visibility of both the production process and the pre-production critical path events. The system has ensured that there is clear visibility of order status. The planning process takes into account customer required dates, material availability, capacity restrictions and also enables any critical path issues to be considered (e.g. sample approvals).
FastReactPlan has allowed Tata to reduce its lead times by understanding their available capacity and maximising production efficiency. In addition, the use of the FastReactPlan’s critical path enables Tata to quickly identify any potential problems, thus empowering them to take corrective actions before problems arise.
“FastReactPlan solution has greatly increased our visibility so that now, should a delay occur anywhere in our supply chain, we can plan around the problem and create the most effective production schedule with just a few drags and drops.
Rodrigo Toledo, Director
“If a production line is running below capacity, this is quickly evident and orders can be easily moved from one line to another to balance the workload and increase production efficiency.”
Tata
The Conclusion
Increased production efficiency has enabled Tata to reduce its workforce by around 20 per cent. In addition, FastReactPlan (Key Performance Indicators) have allowed Tata to accurately measure and hence further improve On-Time Delivery Performance (OTDP). Effective performance monitoring is proving to be the catalyst to truly maximise efficiency, working alongside and complementing lean manufacturing practices.
Rodrigo Toledo, Director at Tata, commented: “We pride ourselves on being able to provide our customers with on-time deliveries, competitive pricing, attention to detail and outstanding service levels. FastReactPlan has played a significant role in allowing us to achieve this and to stay ahead in our game.”
“Since the implementation of FastReactPlan solution, efficiency has measurably improved. We have reduced our lead times, and we have reduced work in progress by more than $100,000 in 6 months.
Rodrigo Toledo, Director
“This is due to clear visibility of what is happening on the factory floor, thus allowing orders to be fulfilled in the most timely and cost-effective manner. We have also virtually eradicated late deliveries.”
Tata
Related testimonials
Americas
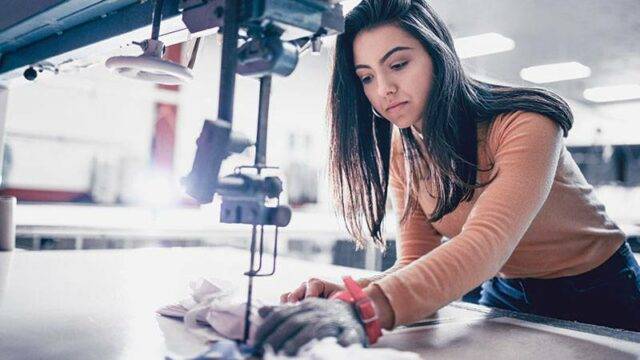
#ProductionPlanning
Rio Sul digitize production planning with Coats Digital’s FastReactPlan
As our industry resets from Covid-19, Mexico’s leading denim manufacturer, Rio Sul, is laying the foundations to win the recovery…
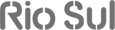
Americas
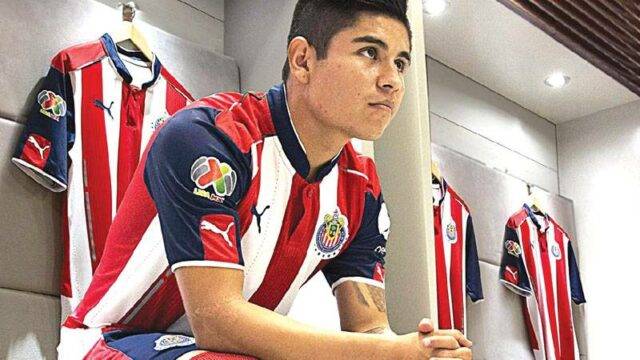
#ProductionPlanning
Industrias MyR supports business growth with FastReactPlan
One of the Latin America’s most recognised sports apparel manufacturers is implementing FastReactPlan to streamline planning processes, improve coordination and…

Americas
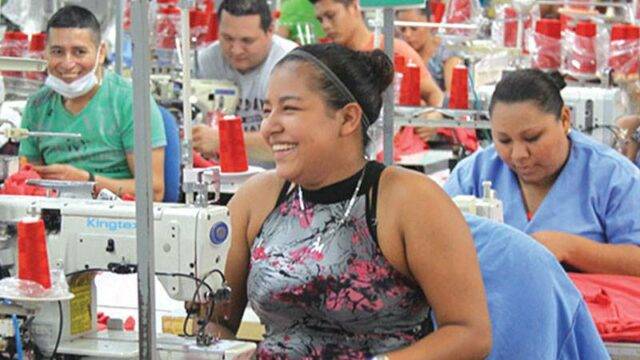
#ProductionPlanning
Pinehurst Manufacturing selects FastReactPlan to provide foundations for business growth
Leading sports apparel manufacturer implements FastReactPlan in Honduras and Nicaragua, to respond efficiently to market demands for increased flexibility and…
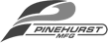